The Pursuit of Streamlined and Scalable Solutions
A CONMED SUCCESS STORY
Advanced technology and innovation are keys to CONMED’s culture and success. The products they develop and solutions they use aim to improve customer experience and enhance outcomes. When the CONMED QA Team was tasked with streamlining their global product development and technical documentation processes, they naturally selected innovative, industry-leading tools. Because of this decision, their latest projects were completed early, well within budget, and met all EUMDR regulation requirements. Best of all, this pattern of success and innovation is poised to repeat thanks to CONMED’s investment in advanced and scalable software solutions from PTC and Oberon Technologies®.

THE HISTORY
For CONMED, innovation is innate. They’ve led the development of cutting-edge surgical and patient care products since 1970. Since its first acquisition in 1989, CONMED has consistently added innovative brands to its global organization, doubling in size with the Linvatec addition in 1997. In 2004 with the acquisition of the gastroenterology and pulmonary business from C.R. Bard, they expanded their presence in the general surgery market. The addition of SurgiQuest in 2016 and Buffalo Filter in 2019 also greatly increased their presence in General Surgery. Today, M&A continues with the additions of In2Bones and Biorez in 2022 which expanded their Orthopedic footprint.
For the QA Team, each acquisition brings new systems and facilities to integrate into the global information ecosystem. When information sharing across global locations and varied systems is absent or requires frequent human intervention, challenges are compounded. “While other organizations may simply add more staff to address the complexities of more systems, we realize that’s not economical or scalable,” says Linda Cohen, Sr. Corporate Manager of Quality Systems. “At CONMED, we run lean, with the ability to scale quickly,” she adds. So, in 2016 when she was tasked with a project to consolidate the global product information systems, she set out to find a solution that would meet the needs of their varied teams and grow with them into the future.
Linda and team started by selecting PTC’s Windchill system as a QMS (Quality Management System) and PLM (Product Lifecycle Management) foundation. While there were many factors considered, Linda says, “we were most drawn to the scalability of the solution.” PTC proved to be a trusted partner and brought in experienced system integrator Kalypso, a Rockwell Company. They aided in the implementation, deployment, and necessary acquired business process changes. The Windchill rollout spanned from May 2018 to December 2018 and QMS from September 2018 to April 2019. As anticipated, CONMED continued to enhance this solution by adopting additional functionality such as RIMS (Regulatory Information Management System) and the SIM (Service Information Management) solution for global documentation.
The PLM implementation took a complicated, inefficient, and convoluted system to a streamlined, state-of-the-art, scalable architecture with Windchill PLM at the core.
However, with success comes new challenges…
A NEW CHALLENGE
The success of the PLM project enticed management to task Linda in late 2021 with reducing translation costs and upgrading their eIFU platform. Once again Linda turned to PTC. This time the recommended partner was Oberon Technologies®. This leading system integrator for content solutions boasted extensive Life Science experience and hundreds of successful implementations.
CONMED’s varied legacy systems and differing IFU processes required extensive manual effort. This resulted in long delays and duplication of work across regions. Additionally, customers found the eIFU site cumbersome. The quality inaccurately represented the experience and innovation of the $1B CONMED enterprise.
It was essential this solution meet CONMED’s technical needs, and more importantly, their customer satisfaction requirements and EUMDR mandates. IFUs had to be accessible in all relevant languages and regions globally. The online eIFU portal had to provide intuitive navigation and robust filtering by region and product. And, it all had to adhere to CONMED brand standards.
THE SOLUTION
THE RESULTS
Within weeks, CONMED had a new eIFU delivery site up and running, well ahead of the anticipated timeline and compliant with all CONMED brand and EUMDR requirements. The new eIFU solution enables 5-minute updates vs 1 hour+, and allows CONMED’s QA Team the ability to administer and sustain the system without increased burden or dependence on other administrators.
The Windchill SIM and Arbortext content solution is on target to achieve at least a 20% reduction in translation costs. It also enables collaborative authoring, further increasing the efficiency of the labeling team. Adopting these advanced, innovative solutions keeps CONMED poised to quickly implement additional automation, making it easier than ever to keep up with continued growth and acquisitions
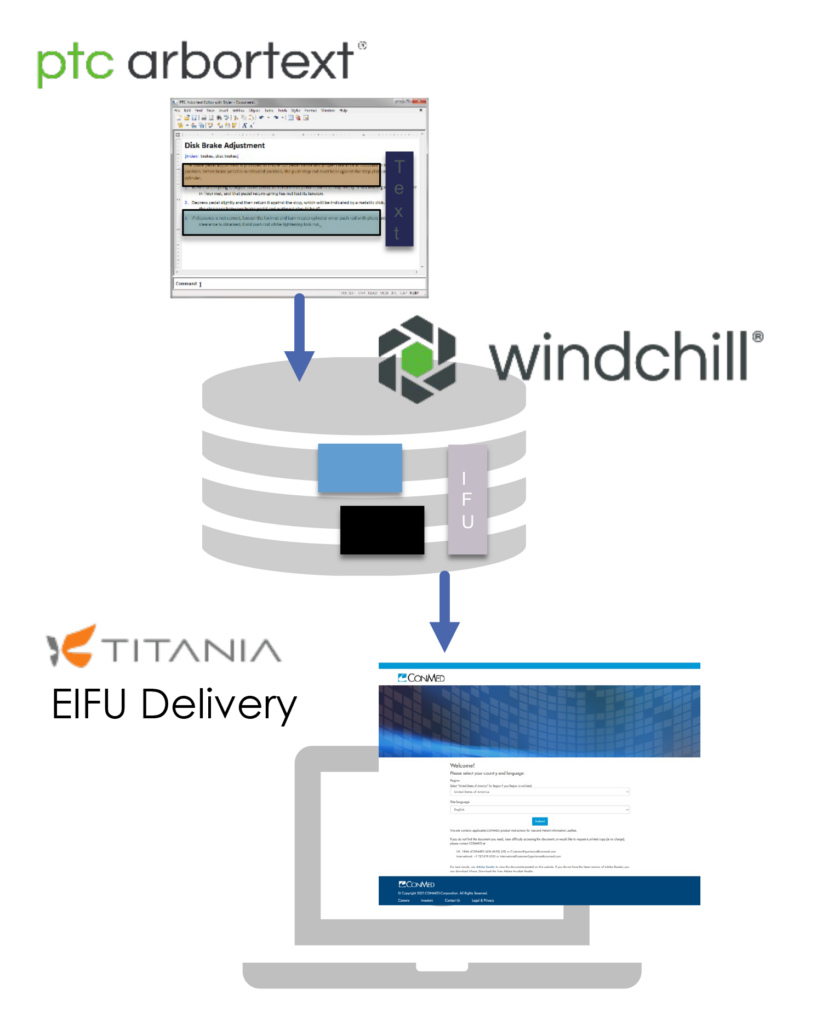
LESSONS LEARNED ALONG THE WAY
Common systems and common processes bring the global team together.
The timing of CONMED’s move to Windchill was serendipitous. Having completed in 2019 before the pandemic shutdowns, Windchill’s ability to promote remote access, online collaboration, and automation was critical during the pandemic and into the future. Before Windchill, global teams worked in silos and change management processes were paper based. And Quality System process required printing of NCR’s out of Oracle or Trackwise for manual completion. With Windchill, team members no longer wait overnight to talk with a CAPA representative in another time zone. Now they can see the information real-time in the CMS. If old processes had been in place during COVID lockdowns, it would have created significant delays and/or halted the release of products making a dramatic impact on revenue. Thankfully, Windchill enabled the team to share visibility and best practices globally and remotely throughout the last two years. With the adoption of a common system and similar processes, they now regularly meet, preventing work in silos. Team members are forming new relationships and partnerships, resulting in support and increased efficiencies globally.
Crawl, Walk, Run – Don’t do it all at once!
While there are many benefits to adopting a scalable system, it is critical to set realistic expectations for each stage. Begin by bringing together all stakeholders (IT, Quality, R&D) before starting a project. Discuss the plan, then move to execute. Level set the initial deployment and how you will scale for each additional stage. Consider the data, process changes, staffing, deployment, and communications needed. Rely on stakeholders from all groups to help make the most informed decision and serve as change agents. Use them to gather feedback across the organization – do not wait to be in pilot before gaining input. This will ensure you move to implementation faster with greater confidence in the adoption and success of your project.
Build Your Team with Talent and Trust
Critical to CONMED’s project success was its partnerships with PTC and Oberon, which according to Linda Cohen and Noah Cumby, Corporate Program Manager, were ideal. “They not only have proven track records, they are dedicated to us for the long term, more like a marriage,” says Linda. These partners recommended tools with all the capabilities we needed and allowed us the time to assess and make a final decision. Noah added “We feel like Oberon gets us; they truly understand what we need. They provide honest feedback, and don’t just always agree with us if they see an issue.” The complexities of adopting global systems requires a trusted and guiding partner. Through their insight you can prioritize tasks, ensure a holistic approach, and establish expectations along the way. A good partner will also help you build the right team, with skills and knowledge needed to ensure ongoing success.
FUTURE INNOVATIONS
The successful implementation of a global information system, lower translation costs, and a more effective global eIFU delivery platform are just the start of the rewards CONMED is realizing from these projects. The stakeholder committees and deployment methods are now being used by other teams as they scope and plan projects, such as consolidating ERP and other business systems. The global collaboration, made possible by a common system, is allowing CONMED to identify new ways to further streamline processes and more quickly integrate acquisitions. The scalability of the PLM, SIM and Titania® Delivery platform provides opportunities to introduce new functionality for years to come, continuing CONMED’s tradition of innovation.